Efficient Cost Tracking in Jewelry Manufacturing with JewelryAdmin
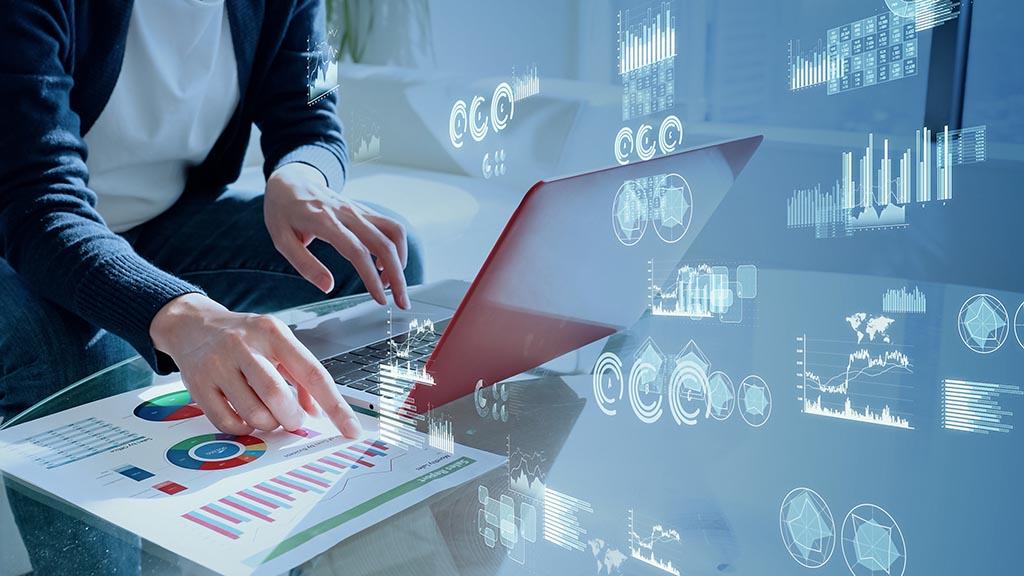
Tracking costs in jewelry manufacturing can be a challenging task due to the constantly fluctuating prices of raw materials and the complexity of the manufacturing process. While input prices like gold can change on a minute-by-minute basis, component prices like gemstones and diamonds are hard to price. On top of that, manufacturers combine many components and labor hours into a new product, making it difficult to track the overall unit price.
This is where software solutions like JewelryAdmin come in handy. As a cloud-based software solution designed specifically for the jewelry manufacturing industry, JewelryAdmin provides businesses with tools that track input costs, labor hours worked, and many hidden costs like gold loss. With real-time visibility into these costs, businesses can make informed decisions about their operations, identify areas where they can save costs, and remain competitive in the industry.
By automating the tracking of input costs, JewelryAdmin allows businesses to track changes in material prices and adjust their pricing accordingly. With real-time visibility into labor hours worked, businesses can accurately calculate their labor costs and adjust their production processes to increase productivity. Furthermore, JewelryAdmin’s tools for tracking gold loss can help businesses minimize waste and improve efficiency, which can result in significant cost savings over time.
It is no secret that all large-scale and profitable companies use software systems to grow. Without these tools, companies can quickly fall behind their competitors and struggle to remain profitable. In today’s fast-paced business environment, where the competition is fierce, it is crucial to have the right tools to succeed.
Tracking costs in jewelry manufacturing can be challenging, but it is a necessary task to ensure profitability. Software solutions like JewelryAdmin provide businesses with the tools they need to track input costs, labor hours worked, and many hidden costs like gold loss. By using these tools, businesses can make informed decisions about their operations, identify areas where they can save costs, and remain competitive in the industry. Without these tools, businesses may struggle to remain profitable and grow in today’s competitive business environment.