JewelryAdmin vs. Competitors: What Sets Us Apart
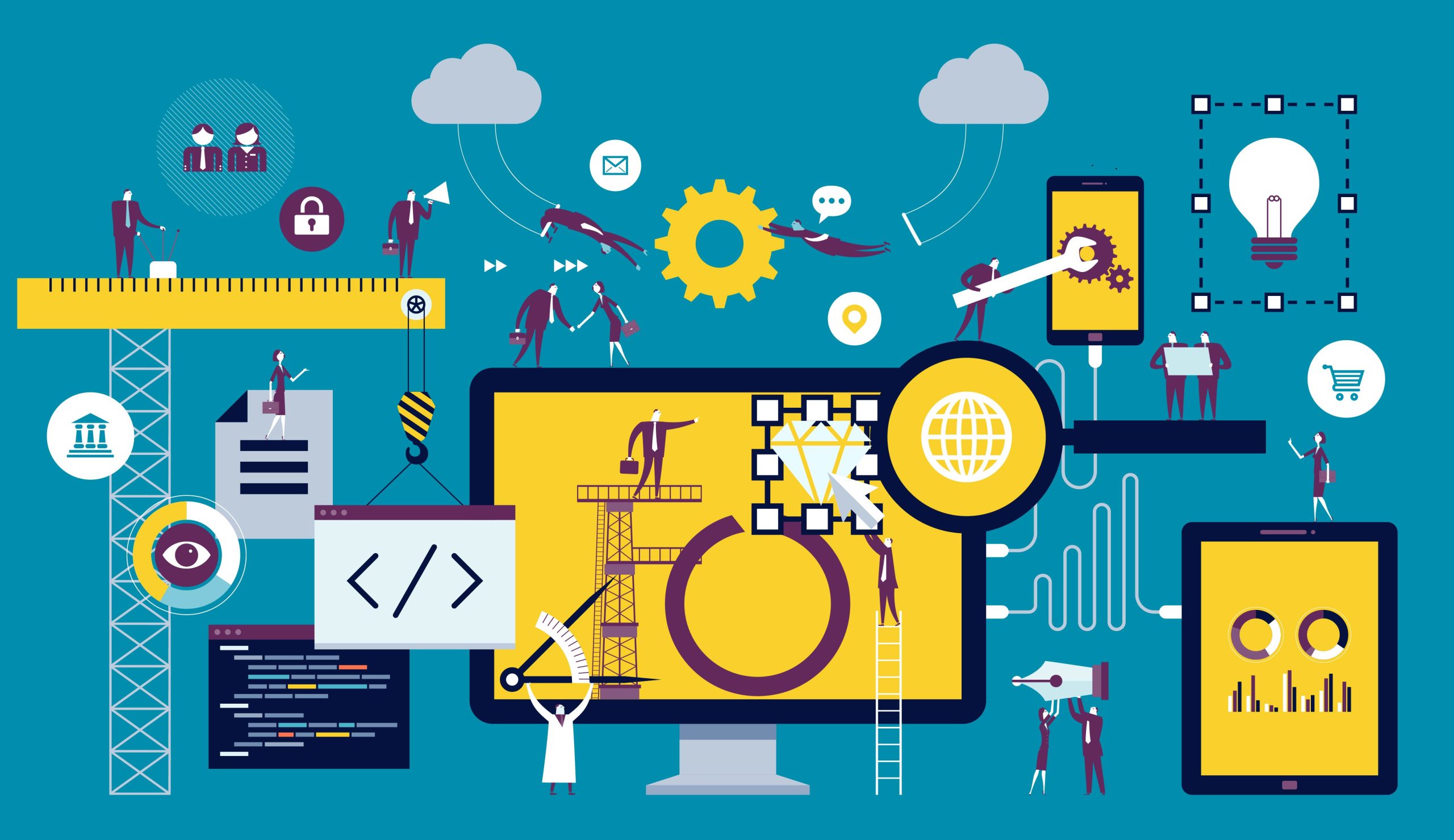
Jewelry manufacturing is an intricate process involving multiple complex steps – from CAD design to casting, polishing and setting precious metals and gems. Streamlining workflows while maintaining quality standards presents numerous challenges. JewelryAdmin provides an integrated software solution built specifically for jewelers’ needs. But how does our platform stand out from competitors? This article examines the key capabilities setting JewelryAdmin apart.
Specialized Industry Focus
Many enterprise resource planning (ERP) tools cater towards generalized manufacturing verticals. In contrast, JewelryAdmin is purpose-built for the niche intricacies of jewelry making. Instead of retrofitting broad software to try accommodating quirks like precious metal tracking, gemstone settings, and mold management, our system is natively designed around domain-specific requirements. This translates to faster implementations and higher ROI.
End-to-End Workflow Integration
Too often, jewelers are forced to cobble together disjointed apps covering only a portion of operations. This leads to gaps, duplicated data entry, and lack of cross-process visibility. JewelryAdmin consolidates inventory management, production scheduling, manufacturing execution, quality control, analytics, and more under one platform. Seamless integration provides total operational control and data unity.
Real-Time Production Monitoring
Many solutions only offer batch tracking of work orders, lacking insight into bottlenecks. JewelryAdmin interfaces directly with equipment to log cycle times and status changes in real-time. Interactive dashboards let staff spot issues immediately, not after the fact. This facilitates proactive corrections and meeting deadlines.
Materials & Inventory Optimization
Jewelry production revolves around precious substances like gold and platinum requiring tight accountability. JewelryAdmin links usage to output while factoring in recoverable scrap and dust residue. Discrepancy alerts trigger corrective steps like improved housekeeping and employee training. Perpetual inventory management also cuts excess stock while preventing shortages.
Alloy & CAD Management
Managing proprietary custom alloys, and digital design files is imperative yet challenging with siloed systems. JewelryAdmin centralizes your intellectual property providing version control, backup, permissions management, and change tracking – preserving institutional knowledge.
Customer Order Transparency
Complex made-to-order manufacturing makes it hard to give clients reliable updates on order status. JewelryAdmin provides customer portals with real-time visibility into quoted vs. expected delivery dates, key milestones completed, and reasons for any changes. This prevents frustration and builds trust.
Automation & Customization
Rigid off-the-shelf systems force companies to reconfigure processes to fit the software. JewelryAdmin enables automating workflows to match your unique environment exactly. Custom fields, screens, reports, integrations and business logic can be tailored at no added cost to boost adoption and savings.
Dedicated Jewelry Expertise
Some vendors provide generic solutions across many verticals, lacking specialized domain expertise. Our staff combines seasoned jewelry manufacturing veterans with software experts. This fusion delivers both deep industry best practices as well as technical innovation tailored for jewelers’ niche needs.
The intricacies of efficiently producing quality jewelry at scale creates complex challenges not easily solved by one-size-fits-all software or DIY database apps. Purpose-built for jewelry makers, JewelryAdmin integrates specialized capabilities from inventory to quality to production optimizations not bolted onto general solutions as an afterthought. Our platform provides unmatched efficiency, visibility, and control benefits that directly impact profitability. To learn more about finding the right jewelry manufacturing technology for your needs, contact us today.